Actually, it is not that new. PMC Pro™ has been introduced by Mitsubishi in 2010, I bought it from Cool Tools in 2011. PMC Pro™ is an alloy of fine silver and copper. 90% silver, 10% copper. As a fan of “pure” fine silver I was a bit apprehensive about this new offering from Mitsubishi. Why should you use another – quite expensive per gram of pure silver – alloy, when cheap and strong sterling silver is widely available? Professional jewelry makers might have shrugged their shoulders: they were already sceptical about precious metal clay as such.
But curiosity took over and I decided to give it a try. The next question was: for what kind of jewelry is this material best suited? The formal-logical approach documented here was very helpful. You should use PMC – Pro or any other kind – only WHERE its use is optimal and the material has a clear advantage over other materials.
Currently there are quite a few Internet resources available about PMC Pro™. After having read some tutorials, for instance, this article in Fusion, Journal of the International PMC guild and a very informative blog by Lora Hart Pro or Con?, I decided to make up the following table:
“-“ Qualities
|
Constraints
|
“+” Qualities
|
Possibilities
|
20% shrinkage
|
no large stones can be co-fired, tricky to estimate future bezel size
|
good workability: does not dry up fast
|
long working time, possible to re-knead several times
|
low melt point (800C), no hard solder can be used, no Oil Paste can be used for repairs!* Not true, read this blog
|
impossible to make multi-component pieces which need step-by-step soldering (from hard to medium to easy), no designs with the risk of cracks, no large stones can be co-fired
|
high tensile strength
|
possible to make rings and (bangle) bracelets, also from one piece, with tiny elements which will not break
|
complicated firing procedure (carbon firing needed)
|
when using combustible components, careful planning of the firing procedure is needed
|
very flexible, high plasticity
|
possible to make sophisticated sculptures
|
does not blend with other PMC
|
combined pieces not recommended
|
easy to attach fresh Pro to fired Pro with homemade slip (add some lavender oil to the slip)* Not true, read this blog
|
possible to make multi-element pieces without Oil Paste
|
dedicated tools needed
|
buy new toolkit, make a series with PMC Pro only
|
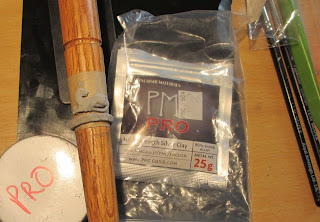
Leave a Reply